Here is a general overview of the steps involved:
Material Preparation: The production begins with preparing the ABS material. ABS is a thermoplastic polymer, and it usually comes in the form of granules or pellets. These pellets are typically loaded into a hopper or feeding system.
Heating and Extrusion: The ABS pellets are melted and heated to a specific temperature in an extrusion machine. The molten ABS is then forced through a die, which gives it the desired shape and dimensions of the shower tray. This process is called extrusion.
Cooling: Once the ABS material has been extruded into the shape of the shower tray, it needs to be cooled and solidified. This can be achieved through various cooling methods, such as passing the tray through a water bath or using cooling fans or chambers.
Trimming and Finishing: After the shower tray has cooled and solidified, it is trimmed to remove any excess material or rough edges. This can be done manually or using automated trimming equipment. The tray's surface may also be smoothed or polished to achieve the desired finish.
Reinforcement (Optional): In some cases, additional reinforcement may be added to enhance the strength and durability of the shower tray. This can involve integrating metal or fiberglass reinforcements within the ABS structure.
Quality Control: Throughout the production process, quality control measures are implemented to ensure that the shower tray meets the required standards and specifications. This may involve visual inspections, measurements, and testing for factors such as dimensional accuracy, structural integrity, and surface finish.
Packaging and Distribution: Once the shower trays have undergone quality control checks and meet the required standards, they are typically packaged and prepared for distribution. This involves protecting the trays during transportation and labeling them for identification.
Besides,During the production of ABS shower trays, several important considerations and precautions should be taken into account to ensure a high-quality and safe end product. Here are some key matters needing attention:
Material Quality: Ensure the ABS material used in production is of high quality and meets the necessary standards. This helps ensure the durability, strength, and resistance of the shower trays.
Mold Design and Maintenance: Proper mold design is essential for achieving accurate dimensions and desired features of the shower tray. Regular maintenance and cleaning of the molds are crucial to prevent defects and maintain consistency in production.
Temperature Control: Maintain proper temperature control during the heating and extrusion process. Accurate temperature settings ensure proper melting, flow, and cooling of the ABS material, leading to consistent tray quality.
Cooling and Solidification: Allow sufficient cooling time to ensure proper solidification and dimensional stability of the shower trays. Adequate cooling prevents warping, deformations, or other quality issues.
Reinforcement Placement: If reinforcement materials, such as metal or fiberglass, are used to enhance the strength of the shower tray, ensure they are properly placed and integrated within the ABS structure for optimal reinforcement effects.
Quality Control: Implement thorough quality control measures throughout the production process. This includes regular inspections, measurements, and testing to verify dimensional accuracy, structural integrity, surface finish, and overall product quality.
Surface Finish and Smoothness: Pay attention to achieving the desired surface finish and smoothness of the shower trays. Proper finishing techniques and equipment can ensure an appealing appearance and user comfort.
Cleaning and Sanitization: Maintain cleanliness and hygiene during the production process. This includes regular cleaning of production equipment, molds, and work areas to prevent contamination or the transfer of impurities to the shower trays.
Compliance with Safety Standards: Ensure that the production process adheres to relevant safety standards and regulations. This includes considerations such as non-toxicity of materials, absence of sharp edges or hazardous elements, and proper labeling and documentation.
Packaging and Handling: Proper packaging and handling of the finished shower trays are important to prevent damage during transportation and storage. Adequate protection should be provided to maintain the quality and appearance of the products.
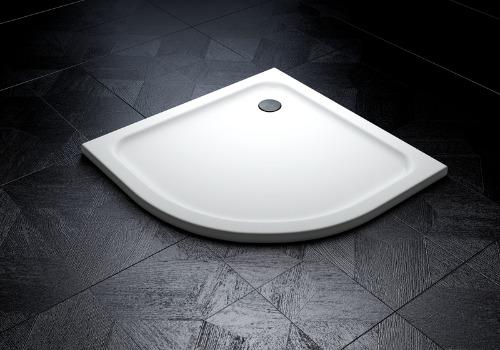
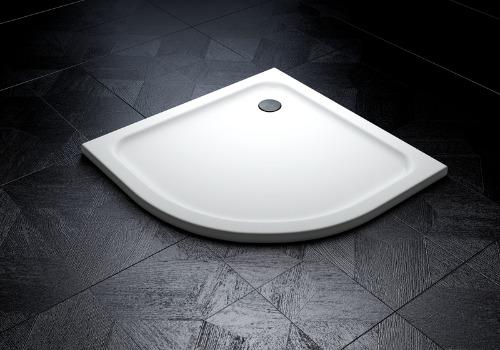