Choosing high-quality raw glass sheets as the starting material is the basis for ensuring the quality of the final product. Next, the original glass sheet is sent to the tempering furnace for heat treatment. In this process, the glass is heated close to its softening point, but not so much that it melts completely. The purpose of heating is to change the internal stress distribution of the glass and improve its strength.
When the glass reaches the predetermined temperature, it is quickly sent to the cooling chamber for quenching. This quenching process is a critical step, which rapidly forms compressive stress on the surface of the glass and tensile stress on the interior. This state of stress distribution gives tempered glass excellent impact resistance and compressive strength.
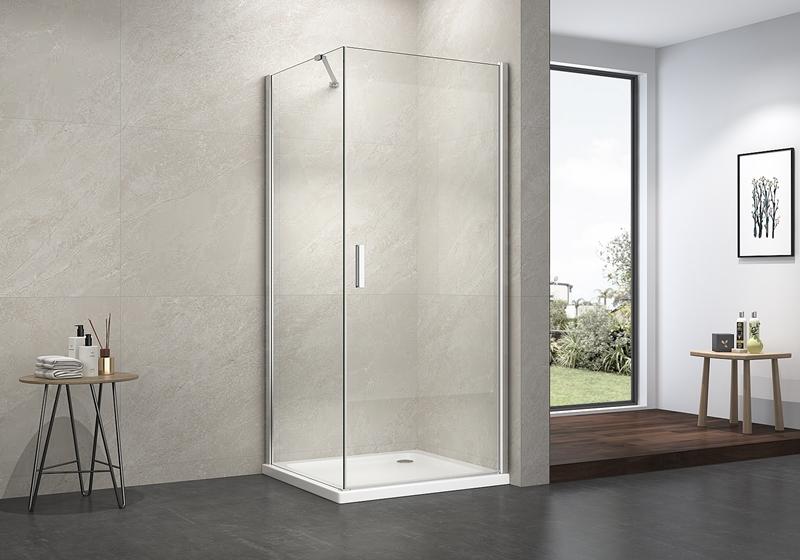
After cooling is completed, perform a quality inspection on the tempered glass to ensure that it has no defects such as cracks and bubbles. Only glass that passes strict quality inspections can be used to make sliding ultra-thin shower enclosures.
According to the design requirements of the shower room, the tempered glass is cut, edged, and punched to obtain shower room glass that meets the size and shape requirements. These processing steps require high-precision equipment and professional technology to ensure processing quality and accuracy.
Through the above production process, the high-strength tempered glass of the sliding slim shower enclosure is made. This kind of glass not only has excellent strength and impact resistance, but also provides good visual effects and tactile experience, creating a safe and comfortable shower environment for users.